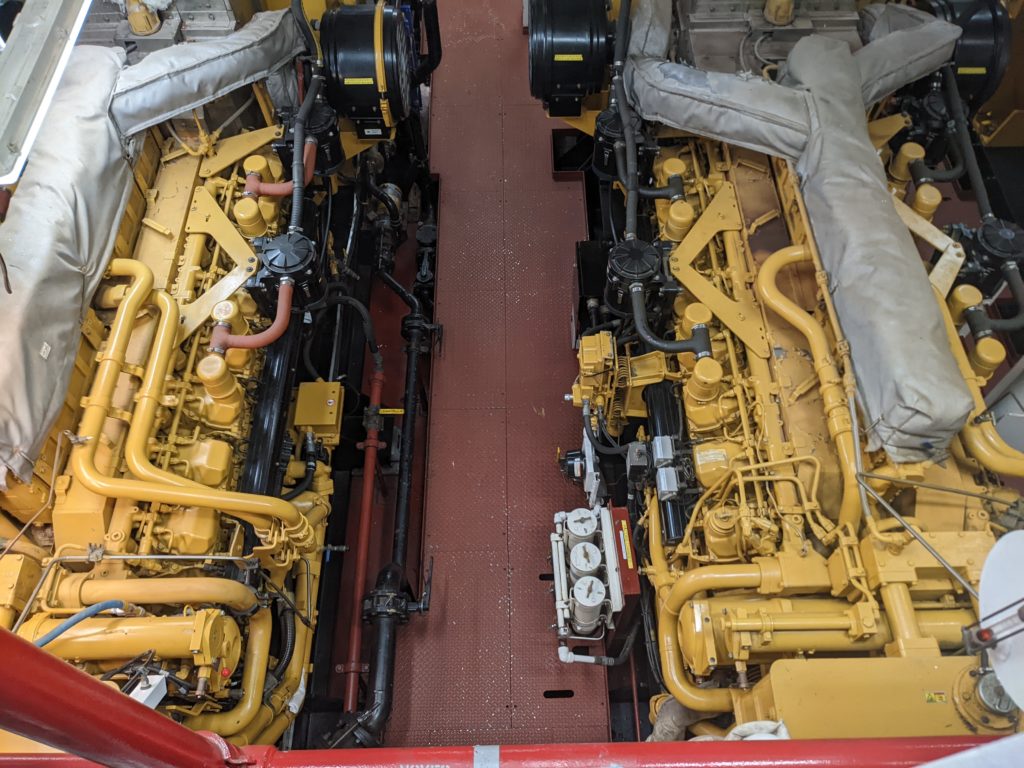
August 30:
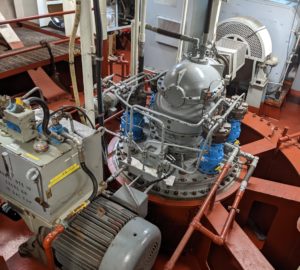
It’s easy to lose track of time while on board. The shifts are 4/8 (4 hours on 8 hours off). I’m working 4:00-8:00 morning and evenings, and I fail to lock down any sort of sleep schedule. Sleep is prescribed “as needed”, hahaha. But this state of mind and body is exhilarating. We are in the thick of things, there’s always something to see, day or night. Nothing in my past couple years has been this stimulating. And when I’m finally depleted from the day, I go right to sleep immediately. Hope my alarms keep working, I’ve had a couple close calls.
The last couple days felt very productive. I exhausted what was immediately available on ship’s cruise share drive related to my video project, so I found James Tilley, an APL Mechanical Engineer on board who is a part of what I’m calling the “Shallow Profiler Team”. He provided me with more detailed drawings on the profiler moorage and the steps for recovery and installation. These documents helped me greatly comprehend what was really going on, and it’s much more involved than I thought previously. I’m understanding why this installation is such a big deal, all of Legs 4 and 5 are devoted to the recovery and reinstallation of this one shallow profiler mooring at Slope Base. I’m excited o be a part of such a big asset to OOI.
We finally got an engine room tour. This ship is done without the incredible engine crew on board constantly monitoring and fixing issues when alarms are raised all below deck. There are four massive diesel generators that constantly run all the ships electricity. The 75,000 gallons of diesel we loaded on before setting off gets converted to all the 480-, 220-, and 110-volt electricity to power all the computers, equipment, and motors, not to mention the 480 V ROPOS as well.
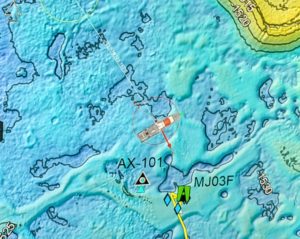
What really interested me is the ship’s drive system, two massive 3,000 hp DC motors coupled to 360-degree azimuth z-drive. Along with the bow thruster, the ship runs its “Dynamic Positioning System” to maintain the ships position. The control system on this ship must be substantial. The crew stated that wind, waves, and position are all tracked as inputs in the control loop to keep the ship within a 1 square meter position on GPS, that’s impressive for a 274 ft research vessel. whisper: I’m pretty sure the ship’s autonomy and control systems are more advanced than ROPOS’.
Most of the recent ROPOS dives involve the deployment of four FETCH tripods forming an acoustic network that can communicate position to the underwater observatory and future AUVs deployed in the area. Much like GPS markers on land, these tripods could tell us when seismic shifts occur at Axial Seamount.
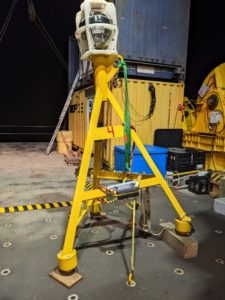
The final FETCH needed an exploratory survey for its position before deployment. ROPOS went down to the initial drop site and found poor terrain conditions, it was too rocky and could prove out of site of the network. So, Dana and the ROPOS drive team decided to try a whole kilometer to the southeast instead. Here’s where some real innovation took place. To get to the new position the team concluded it would be faster to move the whole ship and the deployed ROPOS together to the new location. We moved both vehicles under their own propulsion systems at about 1 kph for an hour. For the TGT to do this while tethered to ROPOS, it used its advanced propulsion systems to move sideways the whole distance because ROPOS was deployed over the port side. It was quite the maneuver, but it got the job done.
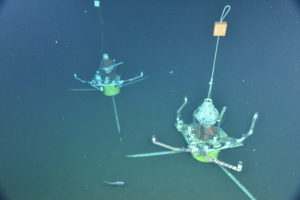
August 28:
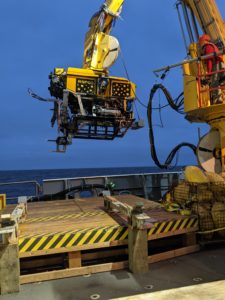
Yesterday was all an 18-hour transit to Axial Base. The whole boat quieted down in terms of research business, not much could be accomplished during the heavily rolling ships movement. I got time on the bow during it. That was fun.
Today I woke up to a finishing a dive in Axial Base to replace the last deep profiler. It’s incredible that research happens around the clock. It’s impossible to see everything. The next dive couple dives got more interesting. We deployed HPIES and Low Voltage Junction Box with its attached CTD, Oxygen, and Spectral absorption sensors. All these assets sit on the sea floor, so it was my first time seeing the bottom of the ocean and it’s 2600 m deep. There is still life down there! So far down all these benthic animals live off the sea columns falling nutrients. Brittle stars, ratfish, jellies, nudibranchs, etc. All of which live down here in the darkness. One rattail fish decided to show off, I’m pretty sure everything down here is blind so it’s impressive it found us.
The highlight of the day, believe it or not was the ascending ROPOS with the old HPIES in tow, during which the ROPOS drive team puts on some tunes and waits while the pressure is off. It’s just a screen of static blue water for 2 hours.
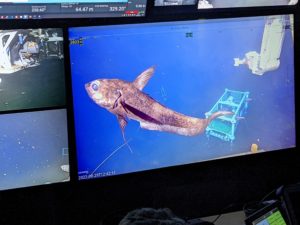
I asked the drive team if I could ask a couple questions about ROPOS while we wait. They happily allowed me to sit right there in front of the controls in between Keith and Luke where I proceeded to ask questions about ROPOS’ arms and thrusters along with comparing it to some of my research in my robotics lab back home. The conversation went on for about an hour, wow it was a real treat.
Oh, I don’t think I’ve mentioned the food yet. Well, it’s fantastic! The cooks prepare full meals with plenty of options and variety. Its way better than the food I usually eat in college. I think I could live on a boat like this for a while. I have yet to be seasick, the food is great, and I’m surrounded by scientists, engineers, and ship crew which are just all my kind of people.
August 26:
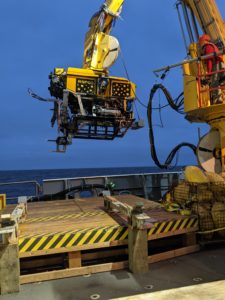
ROPOS is finishing what will probably be one of the longest dives at Slope Base. It’s 2900 m deep and that’s right where the second deep profiler is stationed. Much of the logging process is ascension/descension along the cable, going down is a predicted 4 hours while going up is 2 hours. My team was on watch for when ROPOS made it to the bottom where it cleaned the docking station and detached the Deep Profiler vehicle.
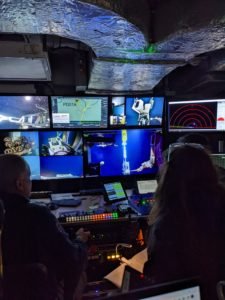
It’s amazing that we can go so deep and have a fast reaction time with the controls, I suppose it isn’t going to change much when the signal always going through thousands of meters of fiberoptic cable.
It’s about time to get started on my project. I’ve been given the entirety of Leg 3 to plan the “How to” video of the shallow depth profiler installation. It looks like I’ll be the lead on the project with other mechanical engineers coming on leg 4. I’m told that this video will be very important information for future scientists because many of the engineers who know the process will be retiring soon. I’ve started writing down the list of names of the people I need to talk to, and how this video may look in general. I’ll need to have a good understanding of everything before the rest of my group comes on board.
I met with Able today to discuss a good way for me to prepare for the project video. He suggested that I look through old dive plans like Visions 21 where there was a previous install, and VISIONS’ 19 with a replacement part. If the dive videos are on board, I should have a look at those as well. I just need to familiarize myself with the old standard installation procedure. Able gave me the printed dive plans for VISIONS’21 to give myself a good start.
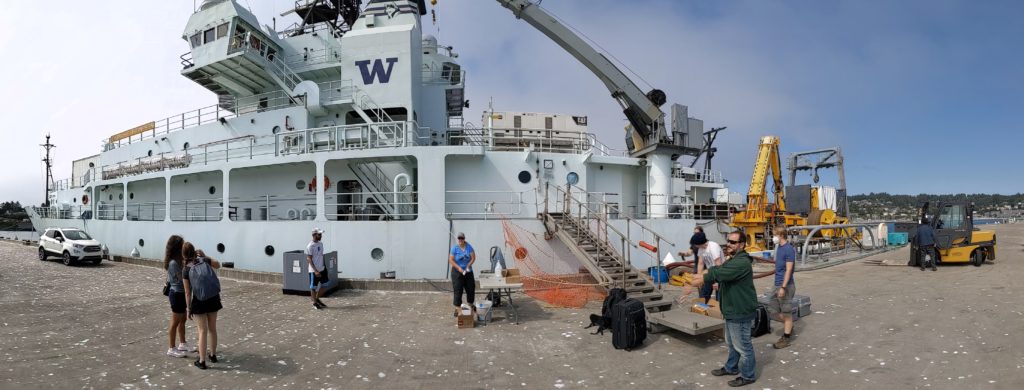
August 25:
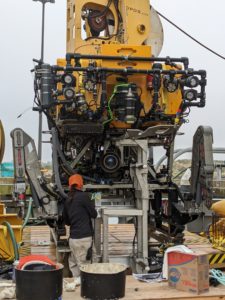
Wow, quite the welcoming on board yesterday. We students boarded the R/V Thompson and received a tour along with getting to know the crew of the ship. Turns out some of the crew of this boat rotates about every three months. I met the Philip, the Second Mate of the ship, who had also just come on board for a crew rotation. It was also his first time on the Thompson, yet he is staying on until November. Previously, Philip had crewed for large shipping vessels and oil tankers. One notable passage/often passage was from Hawaii to southern California. Interesting how the crew of this boat also shifts and changes when they are in port. People just try to get to know eachother.
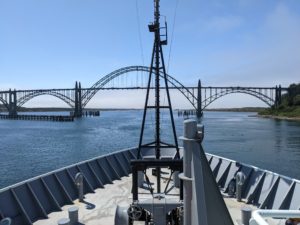
Shoutout to Christina, aka DJ_Ocean on board brought a whole speaker/amplifier/soundboard setup and stationed herself on the main deck for a crew party while in port. Dana on board secured a whole drink fridge for the night. Mixed music where all can meet all was a fantastic way to start the journey.
We just had a tour of ROPOS which involves the control room and the robot itself, so cool. While Ropos is diving we students will be logging observations through the live footage. Peter from Ropos is one othe leading engineers on ROPOS. The team consists of mechanical and electrical engineers as well as drivers. Being a mechanical engineer, I asked Peter some general questions about Ropos and how it operates. The arms of ROPOS are titanium and have 7 axes. Titanium is riddled throughout Ropos to be the main strength when the robot is being used.
We set off the dock very stealthily, no announcements or horns. Some crew didn’t notice while below deck that the ship was no longer tied. Turns out that the ship runs on electric engines with diesel generators. We proceeded to leave port and we experienced the first of what would be a very rollie voyage out to Slop Base.
Anna, Yuliya, Jenna, and I were on watch for the first test dive of ROPOS. We stood behind the ROPOS drive team and took photos while logging the dive. The cameras on ROPOS s are incredibly high quality for the drivers and it was amazing to see all the cameras and drive team working together. Sometimes complications arrive for the dive team such as losing handles on certain tools or running into a heavy amount of marine growth and biofouling.
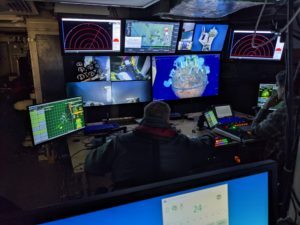
Improvisation seems to be required by all the science and engineering teams to get the job done.